Why Is CNC Tool Selection Important?
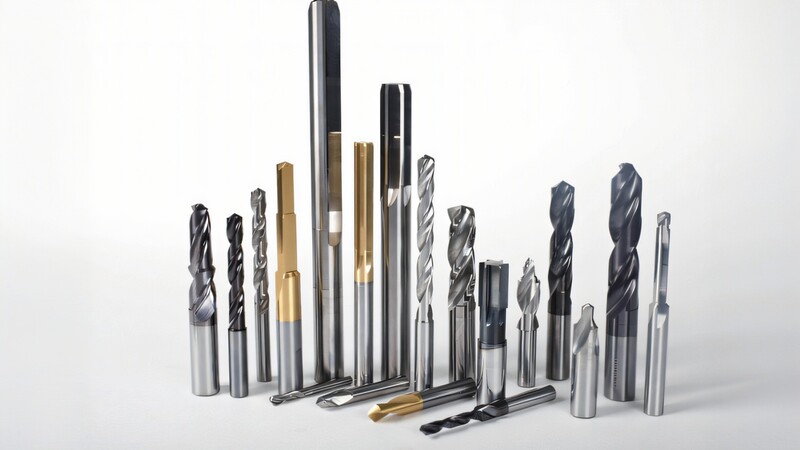
Tool selection is an integral aspect of CNC machining procedures. Various tools used in machining possess different features and intricate geometries. Hence, it is crucial to choose the right one to achieve the best results. With the right machine tools, you can optimize productivity and machining efficiency. Moreover, using the right tools to machine workpieces helps ensure an excellent surface finish of machined parts and reduces tool wear
You might want to make sure you create design features in your part using standard tool size. For example, ensure you design holes in your parts with commonly available drill bits with common measurements rather than a millimeter under or over. Moreover, it would help to ensure the standardization of design features when possible by using a consistent hole size where possible. More importantly, you can effectively design your machined part’s geometry when you know the commonly available tools.
Standard Tool for CNC Machines
CNC machine tools are of different categories, each with specified functions and properties. We will explore the standard tools for CNC machining under the following headings:
CNC Milling Tools
These tools are widely used in machining different parts in the CNC machining arena. They are also regarded as CNC cutting tools. CNC milling tools provide high precision and accuracy. Typical CNC cutting tools include:

- End Mills
End mills are standard tools for CNC milling operations. These CNC tools are highly versatile and quite similar to drill bits. They are suitable for machining holes into workpiece materials without a pre-drilled spot. End mills are available in different types, each of which differs based on the kind of nose or number of flutes they have.
End mills can be classified into three types based on their nose – ball nose (ball end mill), bull nose, and flat end mills. However, 8 is the minimum flute any end mill could have when classifying according to flue number.
- Slitting Saws
A slitting saw is a CNC cutting tool with a flat, circular shape with a hole at the center and teeth on the external diameter. They are also known as slitting or slotting cutters and are often used together with an arbor. A slitting saw is suitable for cutting more material within a small diameter, like slotting or cutoff applications. These saws have unique shapes and geometries, allowing them to cut thin slot-type features on ferrous and non-ferrous parts more efficiently than other tools.
- Slab Mills
Slab mills or cutters are CNC tools suitable for cutting flat surfaces. Their teeth are only on the periphery and are best suited for making wide and narrow cuts.
- Face Mills
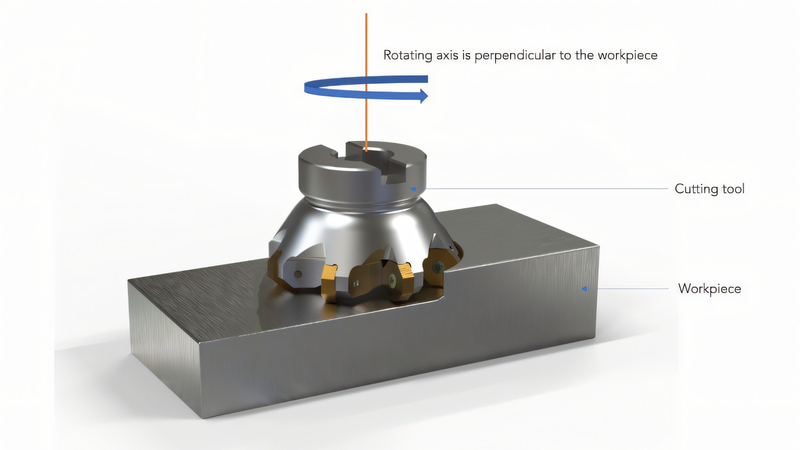
These CNC cutting tools have flat faces with changeable cutting edges made from carbides. CNC face mills can only remove material horizontally since the cutting edges are on the side. The primary function of a face mill is to create flat sections on workpieces. The ability to replace the cutting edges of face mills is one of its many benefits. Consequently, it ensures the extended operating time and tool lifespan.
- Thread Mills
These CNC tools are suitable for cutting threads. Thread mills have similar functions as taps, which machines use to make internal threads. A thread mill can create both internal and external threads. They are your go-to choice when you need to cut through hard materials or asymmetrical parts.
- Fly Cutters
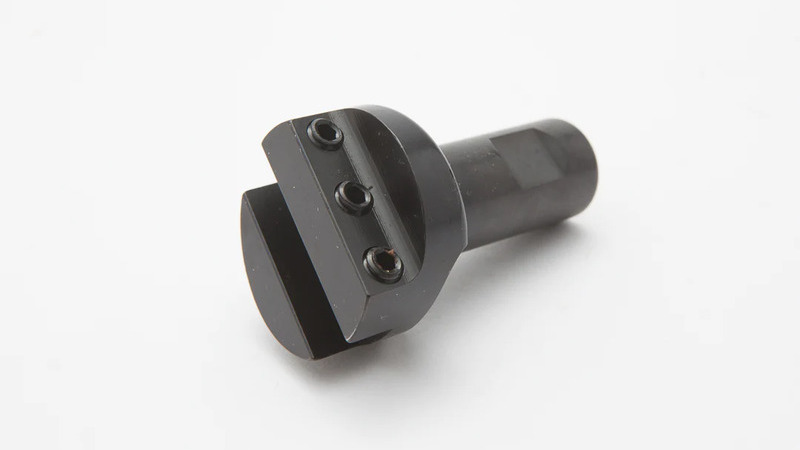
Fly cutters are CNC tools with a solid tool body and one or two cutting bits. The primary function of a fly cutter is to create broad or shallow cuts on workpieces. However, using fly cutters with two cutting bits would be best when machining because they cover larger workpiece sections. Moreover, they are less expensive and sometimes perform the same functions as face mills.
- External Radius Cutter
These are special CNC cutters with semi-circular cutting edges. External radius cutters are perfect tools for adding a radius to the external edge around the rim of a pocket. Machinists often use these tools to smooth uniform workpiece edges, preventing stress concentration and sharp corners.
CNC Turning Tools
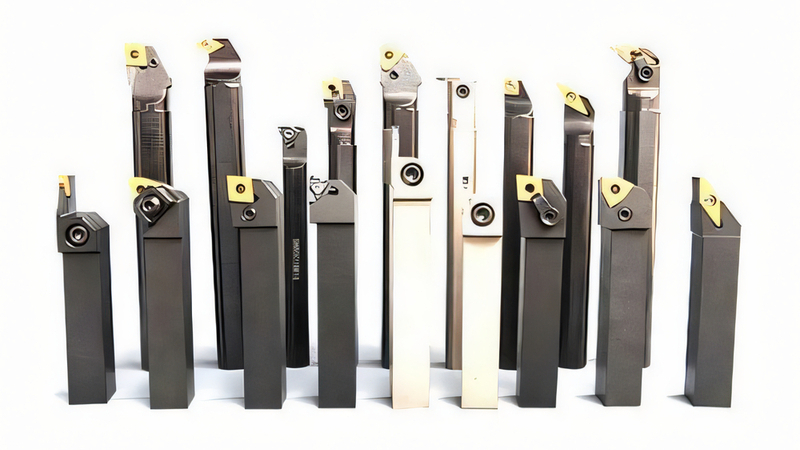
CNC turning tools often work with a turning machine (lathe) that rotates the workpiece at high RPM while the tool cuts the workpiece into the preferred shape. However, the type of tool and turning procedure determines the shape of the machined workpiece. Here are standard turning tools machinists use for CNC procedures:
- Chamfering Tools
Chamfering tools have various applications, including deburring, beveling, and sharp edge removal on machined parts. Its angled cutting surface allows the removal of sharp edges, creating aesthetically pleasing parts.
- Parting Tools
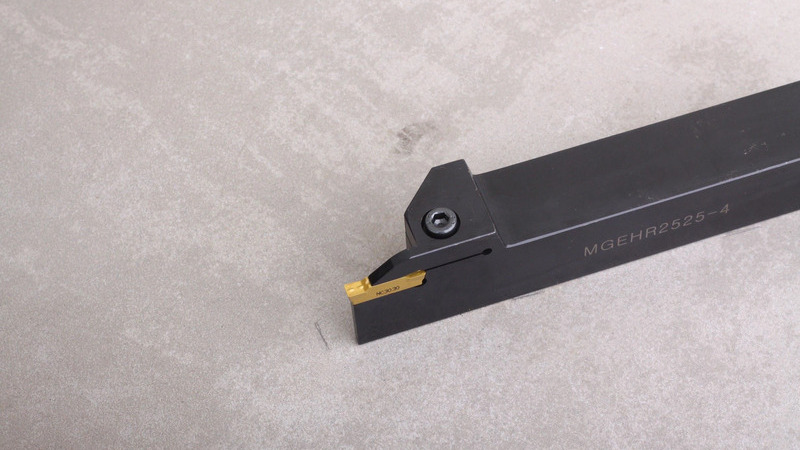
Parting tools are standard CNC tools machinists use in CNC lathes to remove materials from finished parts. This tool has a blade-like cutting edge that cuts the end of the finished part from the rest of the material clamped to the CNC lathe chuck.
- Boring Tools
Lathe boring bars function within a lathe to enlarge pre-drilled, straight, or tapped holes in a workpiece. These boring tools often maintain a single point of contact with the workpiece, facilitating precise hole enlargement. However, note that these boring bars are susceptible to chattering or vibration, which could affect the surface finish of the machined part.
- Knurling Tools
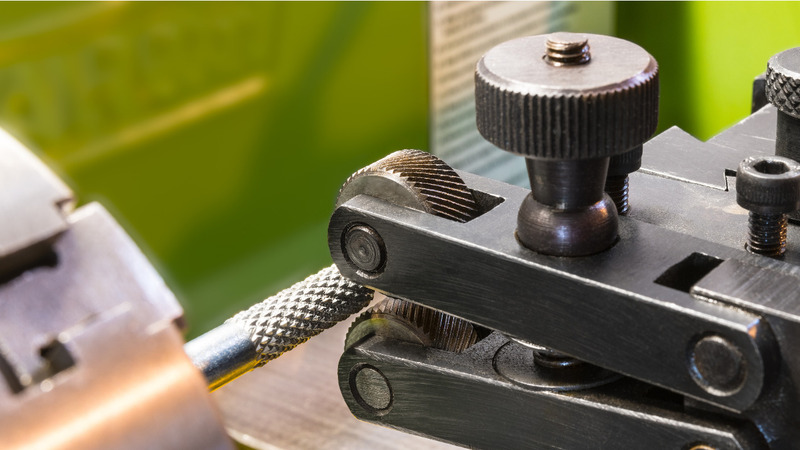
Knurling tools are commonly used to make different attractive ridges or patterns (diamond, diagonal, or straight) on the surfaces of machined workpieces. These patterns help improve the aesthetic appeal and grip on finished products like round nuts, hand tools, and screw heads.
CNC Drilling Tools
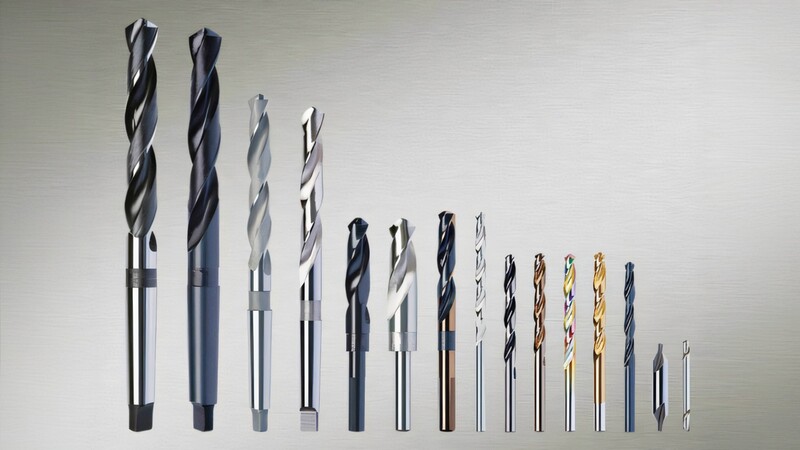
CNC drill bits are standard tools machinists use to make holes of varying dimensions in workpieces. These tools use flutes and tapered cutting points to make holes. Typical drill bits come in three varieties centers, including:
- Center Drills
Center drill bits are CNC tools machinists use to create precise holes in a workpiece before using other drill bits to widen the hole. Machinists use center drill bits to precisely create small spots on a machined part.
- Twist drill (Twist Bits)
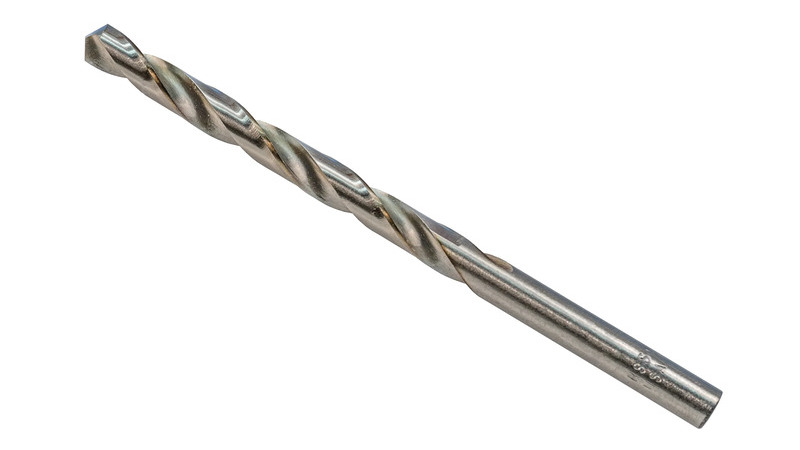
Twist drills are cylindrical drilling tools with spiral/helical grooves. These CNC tools are often made from high-speed steel (HSS) and are suitable for general-purpose machining, especially creating holes in workpiece materials such as metal, wood, and plastic.
- Ejector Drills
Ejector drills are CNC tools commonly used to make larger and deeper holes in workpieces. Machinists often use these tools for deep-hole drilling.
Materials Used in CNC Tool Production
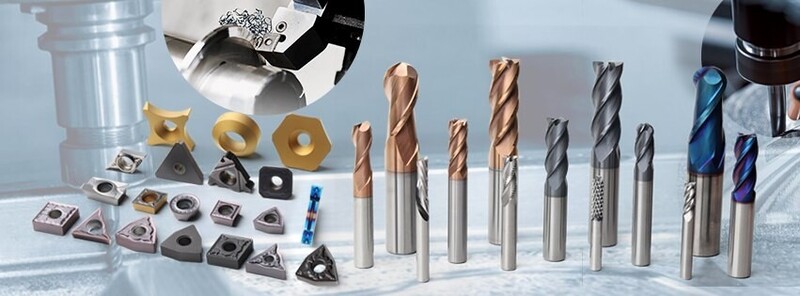
The material used for CNC cutting tools determines vital factors, including the ideal cutting speed and feed rate for machining. Machining experts often recommend using CNC tools made with harder raw materials to cut workpiece material to avoid production inefficiency. Below are typical CNC tool materials:
Ceramics
Cutting ceramics are among the hardest materials used for making CNC tools. These materials are perfect for cutting through the hardest workpiece materials because they are heat and corrosion-resistant. These machining tools have an extended lifespan, like those made with cemented carbide. However, manufacturers scarcely use cutting ceramics for CNC machining tools despite their hardness because they are susceptible to chips and cracks.
Cemented Carbides
Cemented carbides exhibit higher temperature resistance than high-speed steel thanks to their constituents, which include carbide and metals like titanium. However, deformations like cracks or chips on the tool surface can affect their lifespan. Besides, they are not as durable as high-speed steel tools. As such, manufacturers use cemented carbides to make tools for the finishing of machined parts.
High-Speed Steel
Metals such as chromium, tungsten, and molybdenum constitute the high-speed steel. It is a more durable CNC machine tool material. High-speed steel material has a 600ºC melting point and can withstand exposure to high heat levels. Hence, high-speed steel CNC tools are best suited for heavy-duty machining operations.
Carbon Steel
This material comprises a combination of carbon, silicon, and manganese. Besides, it is cheaper than other materials used for CNC machining tools. However, this material exhibits low durability despite offering a significant cost advantage. Moreover, carbon steel tools are unsuitable for heavy-duty machining because of the material’s low melting point of 200ºC. Machinists often use carbon steel tools to cut lightweight workpieces like soft metals, plastics, and foam because they melt faster in heavy-duty applications.
Typical Coatings Used For CNC Tools
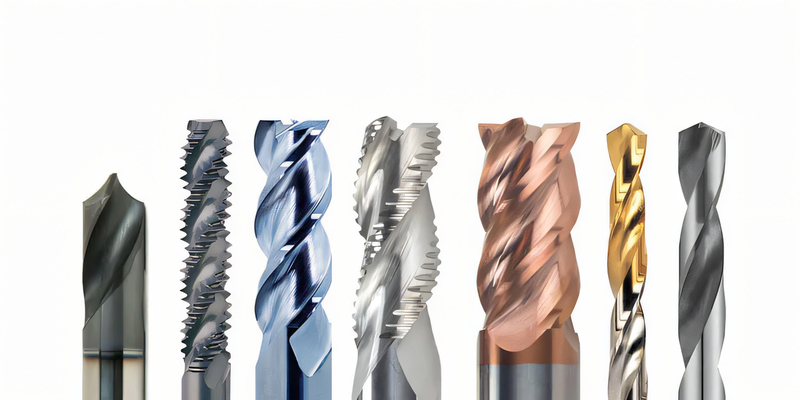
CNC manufacturers coat machining tools with different materials to enhance the tool’s hardness and lifespan. Moreover, coated CNC tools can withstand higher temperatures than those without coatings. Below are the common examples of CNC tool coating:
Titanium Nitride
Titanium nitride is amongst the earliest coatings used to increase the hardness of CNC tools and other properties like wear resistance and thermal stability. This coating type provides moderate oxidation resistance and a longer lifespan. However, manufacturers have strategized variations of this coating with improved properties. Consequently, it is not as commonly used as before.
Diamond
Diamond, the hardest natural material found on Earth, delivers peak performance in demanding machining conditions. As such, it is perfect for various mechanical operations. CNC cutting tools coated with diamonds are ideal for machining challenging materials like silicon-aluminum alloys or graphite.
Chromium Nitride
Chromium nitride is the better tool coating alternative material in cases where titanium nitride fails to yield the desired results. This coating improves the CNC tool’s hardness and resistance to corrosive substances. More importantly, manufacturers employ chromium nitride coatings to enhance the thermal strength of machine tools, making them compatible with high-heat applications.
Titanium Carbo Nitride
Titanium carbo-nitride is a variant of titanium nitride coating. It comprises carbon and is incompatible with high-temperature environments because of its relatively low operating temperature. Nevertheless, Titanium carbo-nitride coating enhances CNC machining tools’ surface lubrication and hardness properties.
Expert Tips for Selecting the Right Tool for CNC
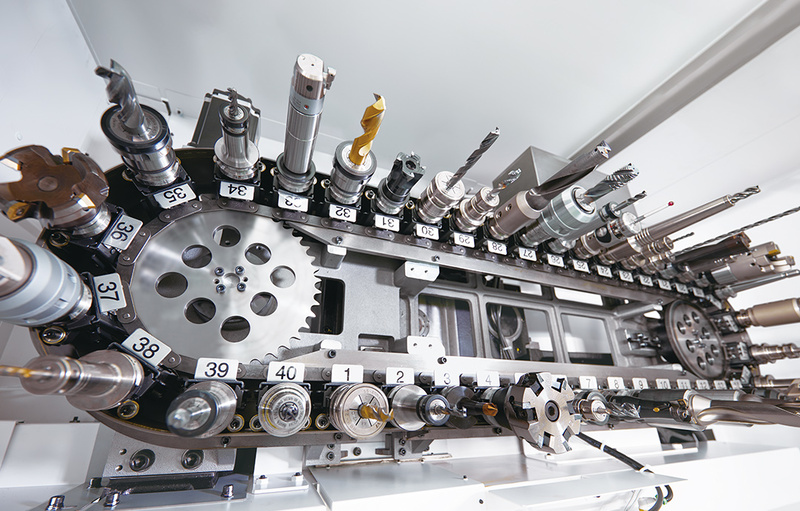
Choosing the right tool for your CNC machining project is critical to ensuring its success. Hence, certain variables must be considered to ensure you choose the right tool for your project. Below are some of these considerations:
The Tool’s Raw Material
The tool’s properties are essential considerations in choosing the right tool for your machining project. For instance, high-speed steel is the ideal tool choice whenever your project requires a tool with an extended lifespan and can handle high heat. Moreover, cutting ceramics is your go-to option if you need a CNC tool to cut extremely hard materials such as cast iron.
The Workpiece Material
Another critical consideration is the intended workpiece’s material. As a general rule of thumb, the machining tool must be harder than the workpiece material to be able to cut it. Hence, it would be best to consider the toughness of the material you intend to work with to choose the appropriate CNC tool material for your machining procedure.
Amount of Flutes
The number of flutes on a CNC tool determines the machine tool’s feed rate. The number of flutes determines the velocity at which the CNC tool engages the workpiece. However, excessive flutes could result in the cut-off workpiece chips getting stuck between the flutes. Therefore, using the optimum number of flutes for your machining operations would be best.
Tool Coating
The CNC tool coating is a critical factor in determining your choice. This coating influences the tool’s properties. For instance, titanium nitride coating increases a CNC tool’s hardness and machining costs. Therefore, titanium nitride tool coating is not ideal if you require a cheap price point.
Type of Machining Operation
Several CNC tools serve different important functions for various machining procedures. As a result, there is a short list of tools compatible with the intended type of machining procedure. Twist, ejector, and center drills are the perfect choice if your parts need holes drilled properly. Thread, slab, face, and slab mills are common CNC tools for workpiece milling. However, the tool for a specific machining procedure can sometimes work for other applications, as in the case of fly cutters.
Conclusion
Tools for CNC machining come in many varieties depending on the required operations and results. Choosing the proper set of tools ensures you reap the vast benefits of CNC machining, ensuring unhinged efficiency and production. This article has discussed all you need to choose the right tool for your machining operations.
AT-Machining is the right expert to entrust your CNC machining operations to for reliable and efficient product manufacturing and finishing services. Our team of professionals can choose the right CNC tools for your product manufacturing. Our CNC machining services include milling, drilling, turning, and Electrical Discharge Machining. We can deliver high-quality, low-volume machined parts and prototypes at competitive prices. Don’t hesitate to contact us now; let experts handle your next machining project! Submit a CAD file today; we provide instant quotes and reliable DFM feedback.